AC Induction Motors
Load and speed variations in rotary electrical machines generally generate oscillations in the electrical signals being sent to them (namely current and voltage). By capturing these minute oscillations and later processing the data, these small perturbations can be matched to their source. Therefore, with a sensor placed at the electrical lines, it is possible to assess many faults generated from electrical, mechanical and process sources, such as:
- Motor and Variable frequency drive performance
- Rotor Bar health, Stator degradation
- cable leakage, Power factor deviation, unbalanced voltage/current
- Harmonic distortion
- Eccentricity, resonance and damaged shaft
- Bearing Defects
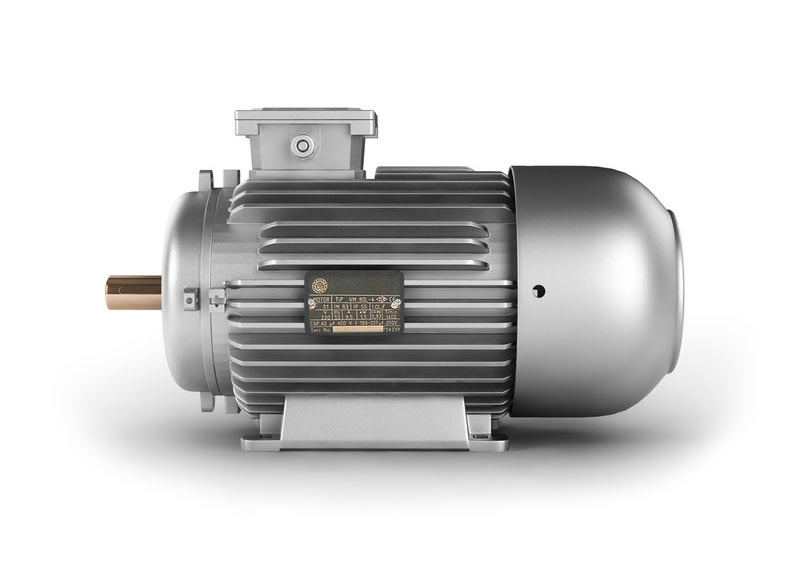
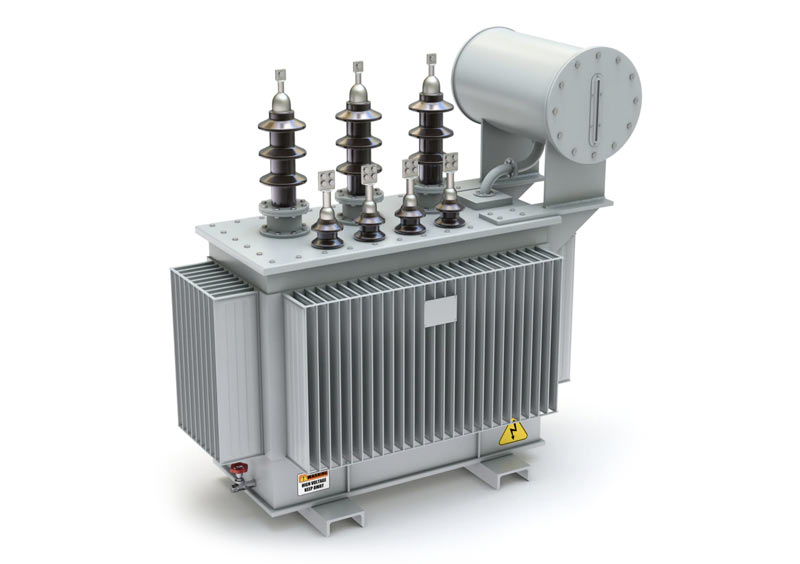
Transformers
Simply from an electrical perspective, transformers behave like electric motors without the moving parts.
Occurring imbalances in voltage, currents, power factors, and harmonics can be assessed similarly to AC induction motors.
Synchronous Motors and Generators
Synchronous motors/generators have similar design and construction as AC induction motors, except that the rotor has an active magnetic field, generated either by permanent magnets or by powering windings in the rotor with DC.
These motors/generators are frequently used in applications that require constant speed, independently from the load, such as reciprocating pumps, compressors, ball mills, and alternators.
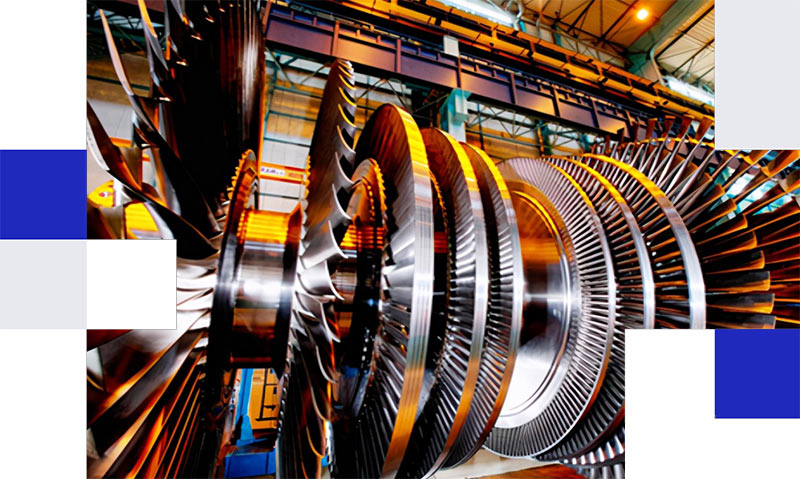
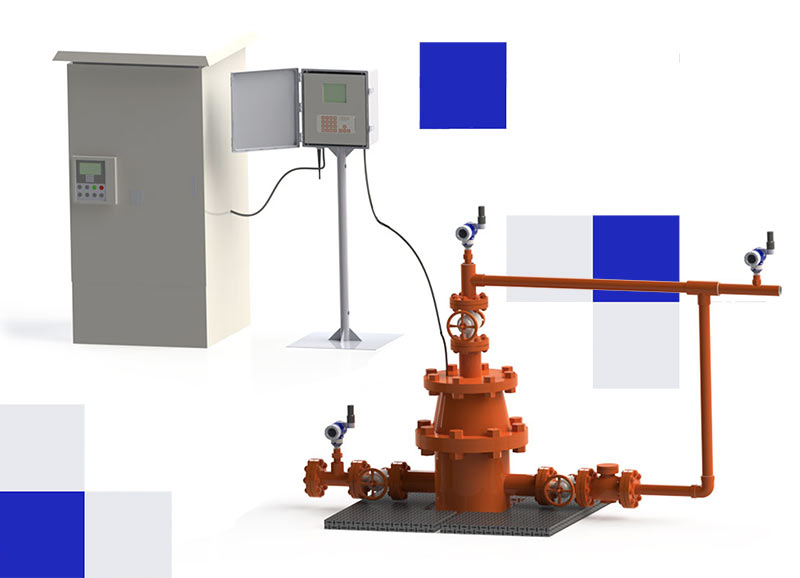
Electric submersible Pumps
ESPs face considerable vulnerability to vibrations caused by flow when pumping multi-phase fluid. This susceptibility is particularly prominent in heavy oil operations where flow-related challenges like free gas from reservoir fluids and steam flashing are common occurrences. Gas locking arises when the pump impellers experience insufficient flow due to a high percentage of gas in the production mixture. On the other hand, steam flash happens when subcooling and ESP speed create vacuum pockets in the impellers.
Our product plays a crucial role in identifying two key aspects:
- (a) Whether there is a high vibration during operation.
- (b) Determining if the source of vibration is electrical, mechanical, or flow-related
Surface Pumps
Surface pumps are not immune to the effects of vibrations, particularly when handling multi-phase fluids. These vibrations can lead to various challenges during their operation.This problem imposes costly intervention for pipeline companies operating with assets located in remote locations.
Our innovative product comes to the rescue by enabling early identification of excessive vibrations during the pump's operation. It offers detailed insights into the source of these vibrations, whether they stem from electrical, mechanical, or flow-related factors. By accurately pinpointing the root cause, our product empowers you to implement targeted solutions, minimizing downtime, and enhancing the overall performance and reliability of your surface pumps.
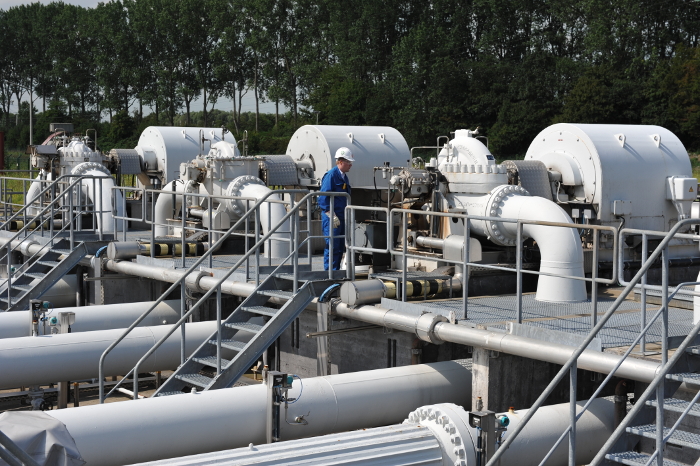

Wind and Tidal Turbines
Turbines are used to drive AC generators, which are essentially constructed as an AC synchronous induction motor, as there is no slip between the synchronous and actual rotation speed. Therefore, the mechanical and electrical performance characteristics can be analysed in the same manner as for AC induction motors.
Belt driven Conveyors
Belt-driven conveyors are widely used in various industries for efficient material handling. However, they are susceptible to specific faults that can disrupt operations and lead to downtime. Understanding these common faults is crucial for effective maintenance and ensuring the smooth functioning of conveyor systems.
- Belt Slippage
- Belt Misalignment
- Belt Tracking Issues
- Excessive Belt Wear
- Material Spillage
- Drive System Problems
- Overloading
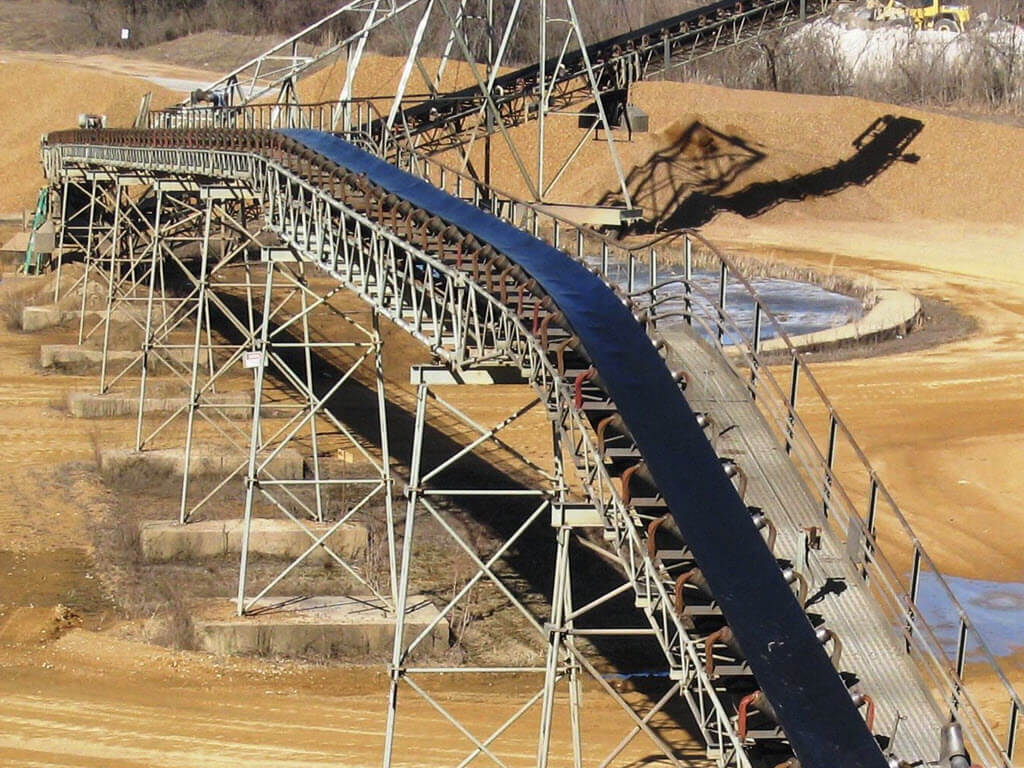
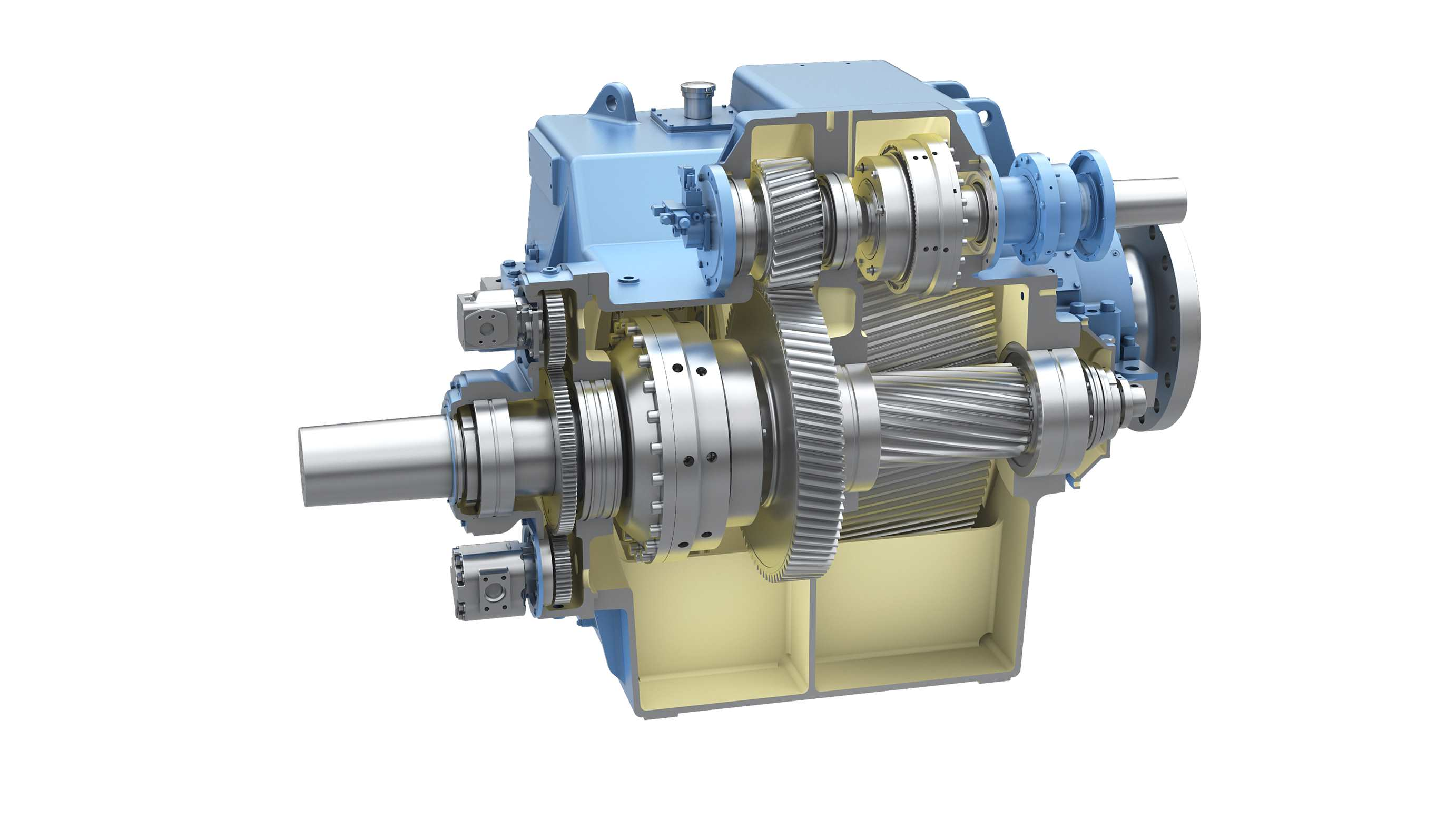
Gear driven electric machinery
Gear-driven electric machinery plays a crucial role in various industrial applications, facilitating power transmission and torque conversion. However, like any mechanical system, they are susceptible to specific faults that can impact their performance and reliability.
- Gear wear and deterioration
- Misalignment
- Inadequate lubrication
- Gear tooth damage
- Excessive noise
- Overloading
- Improper maintenance
Electrical Compressor
All electric reciprocating compressors are becoming the number one choice for compressing gas. However, they impose a high maintenance cost and unplanned downtime.
We offer a condition monitoring system for electric reciprocating compressors which diagnoses many of the common failure modes and quantifies wears on the components.
This fully automated and remote monitoring helps your team to reduce maintenance cost and improve the reliability of reciprocating compressors to an equivalent centrifugal compressor.
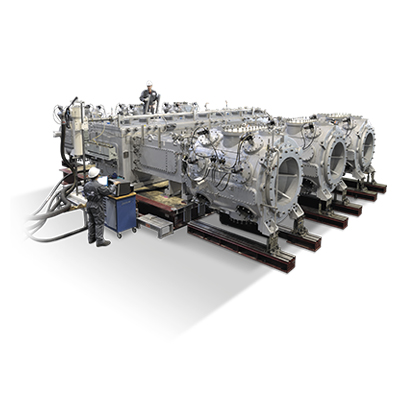
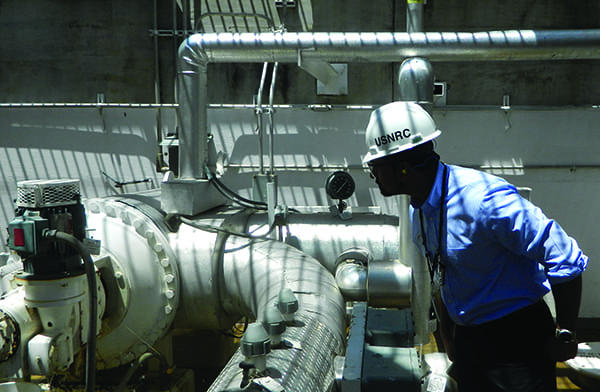
Motor Operated Valves (MOV)
MOV plays a critical role in the the industry.
Our electrical based condition monitoring allows detecting early signs of typical problems, which include:
- Degraded Valve Stem taper, Lubrication, Voltage, Stem-nut
- Wormgear tooth wear and Lubrication
- Obstruction in the valve seat area
- Motor pinion disengagement
- Stem packing adjustments
- Switch Activation
- DC motors and Variable frequency drives
This allows for recommendations for adjustment and modifications to bring the MOV back to their specific performance range.